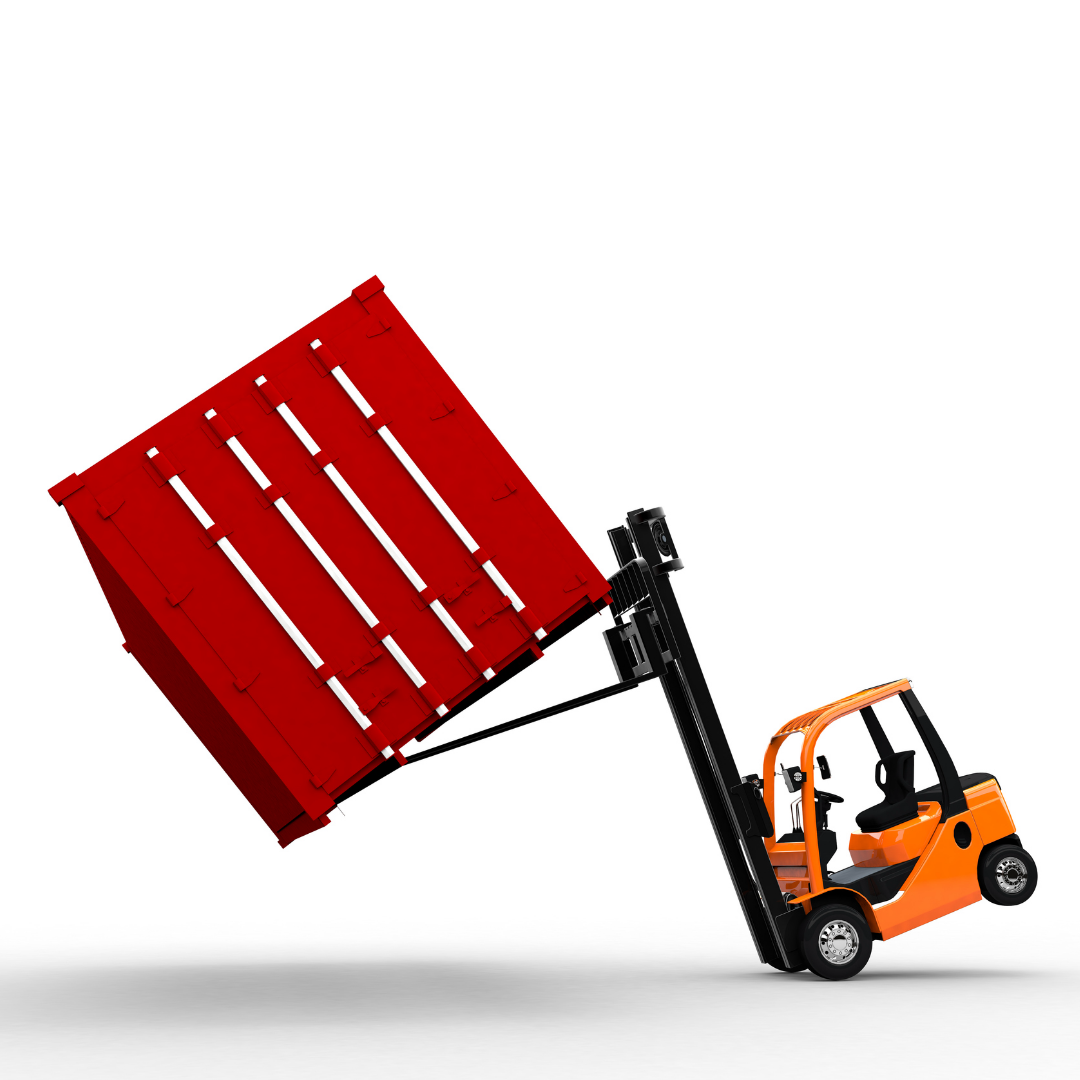
Increasing Forklift Safety: 6 Tips to Prevent Forklift Tip-Overs
Forklifts play a vital role in industries like warehousing and construction, offering the muscle needed to move heavy loads efficiently. However, they also pose serious safety risks. Each year, around 100 people lose their lives in forklift-related accidents, with nearly half (42 percent) of these tragedies caused by tip-overs. These incidents not only result in injuries but can disrupt operations and damage a company’s reputation. So, how can businesses prevent forklift tip-overs? In this blog, we’ll explore effective strategies to reduce the risk of tip-overs, protect operators, and promote a safer work environment. We’ll also discuss what actions to take if a tip-over does happen, including life-saving tips for surviving such incidents.
The Mechanics of a Forklift Tip-Over
Before exploring ways to prevent tip-overs, it’s important to understand what causes them. Forklifts are uniquely designed, with a compact frame and a rear counterweight that keeps them stable during normal operations. However, their steadiness depends on the center of gravity remaining within a specific area called the stability triangle. This triangle is defined by three key points: the two front wheels and the pivot point at the rear axle. When the center of gravity shifts outside the triangle–due to actions like turning sharply with a raised load or exceeding the forklift’s weight capacity–the forklift becomes unstable and can tip it over. By understanding these mechanics, operators can better grasp how their actions impact safety. This knowledge empowers them to make safer choices, reducing the likelihood of accidents on the job.
-
Prioritize Comprehensive Forklift Training
Proper training is the cornerstone of forklift safety. Many tip-overs occur because operators lack sufficient knowledge about how forklifts function, their limitations, and the correct methods for handling loads. Comprehensive training that combines theoretical knowledge with hands-on experience can greatly reduce the risk of accidents. A key focus of training should be understanding load capacity, as overloading a forklift can shift center of gravity and lead to instability. Operators also need to master techniques for safely handling and positioning loads to maintain balance. Driving skills are equally important, particularly when it comes to navigating corners or slopes without compromising stability. To ensure long-term safety, businesses should implement regular refresher courses and periodic evaluations to reinforce safe practices and address any gaps in knowledge. Operators who are well-trained are better equipped to identify potential hazards and respond effectively, making tip-overs and other accidents less likely.
-
Use the Right Forklift for the Job
Different tasks require specific types of forklifts and using the wrong one can increase the chances of a tip-over. For example, forklifts designed for smooth indoor surfaces are not suited for rugged outdoor terrain, and high-capacity forklifts may be unnecessary–and harder to handle–for smaller tasks. Choosing the right forklift starts with evaluating the work environment. Outdoor projects call for rugged models with features that enhance stability, while narrow-aisle forklifts are ideal for maneuvering through tight warehouse spaces. Matching the forklift to the task ensures safer and more efficient operations. Employers should carefully assess the needs of each job and equip operators with forklifts tailored to those demands. This straightforward approach not only minimizes the risk of accidents but also improves productivity and workplace safety.
-
Focus on Load Stability
Improper loading is one of the most common causes of forklift tip-overs. Loads that are unevenly distributed, too heavy, or positioned too high can shift during movement, destabilizing the forklift. Ensuring load stability is essential for preventing accidents and protecting both the operator and nearby workers. To maintain stability, loads should always be centered and kept as low to the ground as possible during transport. Raising a load too high shifts the forklift’s center of gravity, increasing the risk of tipping–especially when navigating turns or uneven terrain. Operators should also avoid sudden movements, such as abrupt stops or sharp starts, as these can jostle the load and reduce stability. Many modern forklifts are equipped with stabilizing features or specialized attachments that help secure loads. By taking advantage of this equipment and following essential safety practices, operators can keep forklifts balanced and significantly reduce the risk of tip-overs.
-
Commit to Regular Maintenance and Inspections
Forklifts are subject to intense daily use, making regular maintenance critical for safe and reliable operation. Worn-out parts or mechanical malfunctions can undermine stability, increasing the risk of accidents. Routine inspections are key to identifying and addressing issues before they lead to serious problems. One crucial area to check is the tires. They should be properly inflated and free from damage to ensure good traction and stability. The hydraulic system also needs to be in top condition to prevent uneven lifting, while the brakes must be fully functional for safe stopping. Additionally, forklift safety features like seatbelts and overhead guards must be operational to protect operators in case of a tip-over. Conducting thorough pre-shift inspections and scheduling regular professional maintenance can keep forklifts in optimal working condition. This proactive approach not only reduces the risk of accidents but also helps extend the lifespan of the equipment, ensuring long-term efficiency and safety.
-
Encourage Cautious and Controlled Driving
Driving habits play a vital role in maintaining forklift safety. Reckless habits like speeding, abrupt turns, and sudden stops can significantly increase the risk of tip-overs. Operators must exercise caution, especially in areas with tight spaces, heavy foot traffic, or uneven terrain. When navigating corners, maintaining a slow speed is critical. High speeds amplify centrifugal force, making the forklift prone to tipping. Similarly, operators should avoid turning while carrying elevated loads, as this can shift the center of gravity and destabilize the vehicle. Smooth, controlled movements are key to keeping the forklift balanced and under control. To support safe driving practices, workplaces should establish speed limits that reflect the unique challenges of their environment. Enforcing these rules fosters a culture of safety, encouraging operators to stay vigilant and prioritize careful handling throughout their shifts.
-
Account for Environmental Factors
Creating a safe working environment is essential for preventing forklift accidents, including tip-overs. Factors like uneven surfaces, obstructions, and hazardous terrain can all increase the risk of instability. Employers play a key role in identifying and addressing these potential dangers to ensure a safer workspace. Slopes and inclines require particular attention. Operators should always drive straight up or down an incline, keeping the load pointed uphill to maintain stability. Turning or driving diagonally on a slope can shift the forklift’s center of gravity, increasing the risk of a tip-over. Similarly, rough surfaces, such as gravel or icy patches, reduce traction, making it harder to control the forklift effectively. In addition to maintaining clear pathways and addressing terrain challenges, proper lighting in work areas is crucial for visibility and accident prevention. By taking steps to eliminate environmental hazards, employers can significantly reduce the chances of forklift tip-overs while promoting a safer and more efficient workspace.
What to Do During a Forklift Tip-Over
While prevention is always the goal, accidents can still happen. How you respond in these situations can make a big difference in preventing serious harm. The most important thing to remember during a forklift tip-over is to stay inside the vehicle. Trying to jump out increases the risk of being crushed under the forklift. Operators should brace themselves by gripping the steering wheel tightly and staying inside the forklift’s protective structure. Once the forklift comes to a stop, the operator should remain calm and signal for help. Supervisors and emergency personnel should be contacted immediately to manage the situation and assist with recovery efforts. Employers should include forklift tip-over response training in their safety programs. Practicing these procedures helps operators react more effectively and confidently during real-life situations, improving safety for everyone on the job.
The Role of Tailift Canada in Forklift Safety
At Tailift Canada, we know that safety is a top priority for businesses that rely on forklifts. That’s why our selection of Tailift forklifts are designed with advanced stability features, ergonomic controls, and durable construction to ensure safe and efficient operations. Along with providing high-quality forklifts, we are committed to supporting our network of dealers with expert advice, maintenance services, and safety resources. By partnering with Tailift Canada, you can enhance workplace safety and minimize the chances of forklift accidents, including tip-overs.
Preventing Forklift Tip-Overs – Strategies for a Safer Workplace
Forklift tip-overs are preventable accidents that emphasize the importance of strong safety measures. By investing in proper training, using the right equipment, maintaining forklifts, and encouraging a culture of caution, employers can reduce risks and create safer work environments. Operators also play a key role by staying alert and prioritizing safety over speed and convenience. Together, these efforts can greatly reduce the chances of forklift tip-overs and keep workplaces productive and secure. While prevention should always be the goal, it’s also important to prepare for emergencies by teaching operators how to survive if they do tip it over. With the right strategies in place, businesses can protect their most valuable asset –their employees.